The term growing on substrates is often used incorrectly. A substrate is synonymous with everything that a plant can grow in or even on. The substrate, or growing medium, therefore serves to keep the plant in place. Examples of substrates are potting compost, coco and rock wool.
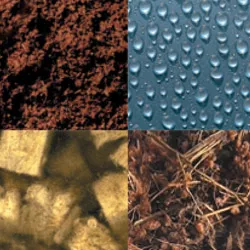
There are basically two methods of cultivating with substrates;
- Run-to-waste
- Recirculation
In a run-to-waste cultivation system the feed water passes the roots just once and is then disposed. This is in contrast to other systems where the drainage water is reused, for example in the so-called recirculation systems.
In run-to-waste systems we make a distinction between substrates that interact with and substrates that don’t. A well-known feeding substrate is potting compost. Other substrates can retain nutrients. coco coir is such a substrate, its feeding and nutrient retention properties differ from potting compost.
CANNA has developed the CANNA TERRA range for cultivating on potting compost. CANNA COCO is for cultivating on coco. CANNA HYDRO is for substrates that retain or release almost no substances: the so-called inert substrates.
Run-to-waste with inert substrates
If you choose to cultivate in a run-to-waste system in combination with an inert substrate, you are choosing a growing method that guarantees high yields. After all this – in combination with rock wool as inert substrate – is the most widely used cultivation method in professional horticulture in the Netherlands. However, this is certainly not the easiest growing method, and you will only be able to achieve high yields with the same professional approach.
The advantage of this growing method is that you know the exact composition of the feed water and so you know exactly what your plants are being fed. However, the drainage water goes directly into the environment, so it is very important that the nutrition you choose is designed for this growing method. Only then you can be sure that the minimum possible residue materials will enter the environment. CANNA HYDRO has been specially designed for this method of growing.
Advantages and disadvantages of hydro cultivation
The advantages of hydro cultivation include being able to accurately manage the nutrients, the amount of water given and the pH. But there are many more advantages. You will experience almost no problems with potting mix related diseases or weeds; the substrates used for hydro cultivation are weed and disease free, and this is why they are often referred to as sterile. Additionally measuring the pH and the electrical conductivity (EC) in the growing medium is simple. The electrical conductivity gives an estimate of the total amount of dissolved salts.
A disadvantage of hydro cultivation is that the substrate used is not always reusable or recyclable. Other disadvantages include the higher initial costs for the substrates themselves and the equipment required. But you can be sure to earn this back in the yields you achieve.
Table 1: Overview of advantages and disadvantages of run-to-waste with inert substrates:
Open system (run-to-waste) | Closed systems (recirculating) | |
---|---|---|
Advantages | Plants receive continuously supply of fresh nutrients. Also suitable for cultivation with 'poor' water quality (EC of 0.75 or higher) |
No need to dispose via drainage. Plenty of air available to the roots |
Disadvantages | More loss of water and nutrients. Need to dispose of drainage water |
Diseases can spread throughout the system via the feed water. pH and EC values in the nutrients have to be monitored more closely |
Nutrients | CANNA HYDRO | CANNA AQUA |
History of rock wool
How rock wool was discovered is not exactly known, one story goes as follows:
Rock wool was discovered by accident in 1840. After climbing a volcano in Hawaii researchers saw long, white threads hanging from the trees. The local inhabitants believed that these were God’s hairs which he pulled out of the volcano when he was displeased. However, investigation showed that the hairs of God were in fact Diabase, a liquid volcanic rock that was cooled and blown apart by the wind after leaving the volcano.
Nowadays rock wool is manufactured in factories. The volcanic rock is ground and pulverised to grit. This grit is then heated to 1500 °C, at this temperature it melts. This viscous substance is then poured onto a rapidly rotating sheet. This forms droplets and each droplet is stretched into a long fibre. These fibres are cured in a kiln and then consolidated into slabs of rock wool. Any shape finished product can then be cut to size. In this process 1 m3 of raw slaberial becomes no less than 90 m3 rock wool. Besides the applications for thermal, fire and sound insulation, in the early 1970s it was discovered that rockwool could also be used as a good growing medium for plants. It was first used on a large scale for cultivation in the Netherlands in 1975.
The rock wool used in construction for thermal and sound insulation is not suitable for cultivating plants. This is because mineral oil is added to make the slaberial water-repellent.
A rock wool variant has been specially developed for horticulture which can actually absorb and retain large quantities of water. This rock wool has considerable capillary capacity, in other words, rock wool can retain large volumes of water. This type of rock wool can retain up to 80% water and still contain 15% air. The remaining 5% is the rock wool itself.
Because each crop has different requirements, different types of rock wool have been developed. The main differences are in the structure of the fibres, horizontal or vertical, their thickness and density. Rock wool is available in various shapes and sizes; for example small plugs or cubes, for germination and propagation, in which seeds or cuttings can take root. These cubes fit into blocks where the young plants can continue to grow. There are also slabs in all imaginable dimensions. These are also known as slabs on which you can place the blocks with young plants.
Many plants don’t like having 'wet feet'. A rock wool slab that is too soft will retain too much water, and one that is too hard will provide too much resistance to the growing roots. A hard slab means that the plant spends a great deal of its energy developing roots – energy that the plant can better use for growing above ground. Therefore the ideal rock wool slab is not too hard and has a horizontal structure so that there is ample volume available for root growth. The quality of a plant is largely determined under the ground, in fact 50%, so the bigger the root volume, the healthier the plant and the higher the yield.
Most rock wool slabs are wrapped in plastic, which makes them easy to pre-soak. The patches that remain dry during the pre-soak will not get any wetter during cultivation; so it is important to work carefully in the pre-soaking phase.
Red and yellow iron
One aspect of growing that is often forgotten is the waste feed water that drains into the sewerage system. The drainage water from CANNA HYDRO nutrients does not contain any serious pollutants, so the burden on the environment is minimal.
Another significant difference between CANNA HYDRO nutrients and other products for run-to-waste cultivation is the raw slaberials used. Because CANNA carefully selects the purest possible raw slaberials for its products there are considerably fewer heavy metal particles in the drainage water. Another important difference with other run-to-waste products is that the CANNA HYDRO nutrients recipe does not contain any red iron. The notion that red iron is more easily absorbed by plants is only valid at higher pH values; the pH range maintained in run-to-waste cultivation systems is too low. Large quantities of red iron are added to many products to ensure that there is sufficient iron for the plant to absorb, but much of this iron is not taken up by the plant. So instead of red iron, CANNA uses a special yellow variant in its HYDRO products. This yellow iron variant is absorbed well by the plant at the pH in the root environment. So considerably less yellow iron is needed than of the widely-used red iron.
The idea that run-to-waste systems are more harmful to the environment than recirculation systems is therefore not entirely correct. There is waste water in both systems; a constant trickle in run-to-waste systems and in recirculation systems a relatively large amount from time to time. The amount of waste water depends on the watering system and the dryness of the substrate, a dry substrate requires more feed water than a wet substrate, and thus not on the type of cultivation system.